Articles & Issues
- Language
- english
- Conflict of Interest
- In relation to this article, we declare that there is no conflict of interest.
- Publication history
-
Received October 21, 2023
Revised February 5, 2024
Accepted April 8, 2024
-
This is an Open-Access article distributed under the terms of the Creative Commons Attribution Non-Commercial License (http://creativecommons.org/licenses/bync/3.0) which permits unrestricted non-commercial use, distribution, and reproduction in any medium, provided the original work is properly cited.
Latest issues
Thermo-hydraulic Effect of Tubular Heat Exchanger Fitted with Perforated Baffle Plate with Rectangular Shutter-type Deflector
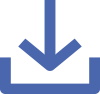
Abstract
A study was conducted on a tubular heat exchanger to improve its heat transfer rate by using a novel baffle plate design with discontinuous swirling patterns. The design consisted of perforated baffle plates with rectangular air deflectors positioned at varying angles. The tubes in the heat exchanger were arranged in a consistent alignment with the airflow direction and exposed to a uniform heat flux on their surfaces. Each baffle plate included sixteen deflectors inclined at the same angle and arranged in a clockwise pattern. This arrangement induced a swirling motion of the air inside a circular duct where the heated tubes were located, leading to increased turbulence and improved heat transfer on the tube surfaces. The spacing between the baffle plates was adjusted at different pitch ratios, and the Reynolds number was controlled within a range of 16,000 to 29,000. The effects of pitch ratios and inclination angles on the heat exchanger's performance were analyzed. The results indicated that using a baffle plate with rectangular deflectors inclined at 30° and a pitch ratio of 1.2 resulted in an average increase of 1.29 in the thermal enhancement factor.
References
Review of Vortex Amplifier Design in the Context of Sellafield
Nuclear Operations. Proceedings of the ASME 2009 12th International Conference on Environmental Remediation and Radioactive Waste Management, Vol. 2. Liverpool, UK, 161-183.
ASME (2009).
2. Abdullah A. Azhari, Ahmad H. Milyani, Nidal H. Abu-Hamdeh,
and Amira M. Hussin, “Thermal Improvement of Heat Exchanger
with Involve of Swirl Flow Device Utilizing Nanomaterial,”
Case Studies in Thermal Engineering, 44, 102793(2023).
3. Wang, J., Wang, Y. and Han, J., “Experimental Investigation on
Separation Characteristics of Axial Cyclone Separator,” Sci.
China Technol. Sci., 2023.
4. Skripkin, S. G., Sharifullin, B. R. and Naumov, I., “Dual Vortex
Breakdown in a Two-fluid Whirlpool,” Sci Rep., 11, 23085(2021).
5. Sheha, A., Ibrahim, K. A., Abdalla, H. A., El-Behery, S. M. and
Sakr, I. M., “Improvement of the Axial-Jet-Pump Performance
using Modified Mixing Chamber Configuration and Inlet Swirling Flow,” Scientia Iranica, 2023.
6. Lv, P., Zhang, Y., Wang, Y. and Wang, B., “Experimental Investigation on the Influence of Swirl Ratio on Tornado-like Flow
Fields by Varying Updraft Radius and Inflow Angle,” Atmosphere., 14(9), 1425(2023).
7. Bai, W., Liang, D., Chen, W. and Minking, K., Chyu Investigation of Ribs Disturbed Entrance Effect of Heat Transfer and
Pressure Drop in Pin-fin Array,” Applied Thermal Engineering,
162, 114214(2019).
8. Chen, Z., Wang, H., Zhuo, J. and You, C., “Experimental and
Numerical Study on Effects of Deflectors on Flow Field Distribution and Desulfurization Efficiency in Spray Towers,” Fuel
Processing Technology, 162, 1-12(2017).
9. Khetib, Y., Alahmadi, A. A., Alzaed, A., Azimy, H., Sharifpur,
M. and Cheraghian, G., “Effect of Straight, Inclined and Curved
Fins on Natural Convection and Entropy Generation of a Nano
fluid in a Square Cavity Influenced by a Magnetic Field,” Processes, 9(8), 1339(2021).
10. Lu, Z., Tao, R., Yao, Z., Liu, W. and Xiao, R., “Effects of Guide
Vane Shape on the Performances of Pump-turbine: A Comparative Study in Energy Storage and Power Generation,” Renewable Energy, 197, 268-287(2022).
11. Liu, F. and Zhang, G., “Study on Melting and Solidification Performances Improvement of Phase Change Material Using Novel
Branch Fin Structure,” Journal of Energy Storage, 63, 107097
(2023).
12. Hussein, M. A. and Hameed, V. M., “Experimental Investigation on the Effect of Semi-circular Perforated Baffles with Semicircular Fins on Air–Water Double Pipe Heat Exchanger,” Arab J
Sci Eng., 47, 6115-6124(2022).
13. Bahuguna, R., Mer, K. K. S., Kumar, M. and Chamoli, S., Entropy
Generation Analysis in a Tube Heat Exchanger Integrated with
Triple Blade Vortex Generator Inserts, Energy Sources, Part A:
Recovery, Utilization, and Environmental Effects, 2021.
14. Ajarostaghi, S. S. M., Karouei, S. H. H., Alinia-kolaei, M., Karimi,
A. A., Zadeh, M. M. and Sedighi, K., “On the Hydrothermal
Behavior of Fluid Flow and Heat Transfer in a Helical DoubleTube Heat Exchanger with Curved Swirl Generator; Impacts of
Length and Position,” Energies, 16, 1801(2023).
15. Keat Goh, L. H., Hung, Y. M., Chen, G. M. and Tso, C. P., “Entropy
Generation Analysis of Turbulent Convection in a Heat Exchanger
with Self-rotating Turbulator Inserts,” International Journal of
Thermal Sciences, 160, 106652(2021).
16. Rahman, M. A. and Dhiman, S. K., “Performance Evaluation of
Turbulent Circular Heat Exchanger with a Novel Flow Deflectortype Baffle Plate,” Journal of Engineering Research, 100105(2023).
17. Rahman, M. A. and Dhiman, S. K., “Investigations of the Turbulent Thermo-fluid Performance in a Circular Heat Exchanger
with a Novel Flow Deflector-type Baffle Plate,” Bulletin of the
Polish Academy of Sciences Technical Sciences, 2023.
18. Rahman, M. A., “Study the Effect of Axially Perforated Baffle
Plate with Multiple Opposite-oriented Trapezoidal Flow Deflector in An Air–water Tubular Heat Exchanger,” World Journal of
Engineering, 2024.
19. Rahman, M. A., “Experimental Investigations on Single-Phase
Heat Transfer Enhancement in an Air-To-Water Heat Exchanger
with Rectangular Perforated Flow Deflector Baffle Plate,” International Journal of Thermodynamics, 1-9(2023).
20. Rahman, M. A., “Effectiveness of a Tubular Heat Exchanger and
a Novel Perforated Rectangular Flow-deflector Type Baffle Plate
with Opposing Orientation,” World Journal of Engineering, 2023.
21. Rahman, M. A., “Thermo-Fluid Performance Comparison of an
In-Line Perforated Baffle with Oppositely Oriented RectangularWing Structure in Turbulent Heat Exchanger,” International
Journal of Fluid Mechanics Research, 2024.
22. Rahman, M. A., “The Effect of Triangular Shutter Type Flow Deflector Perforated Baffle Plate on the Thermofluid Performance of a
Heat Exchanger,” Heat Transfer., 53, 939-956(2024).
23. Rahman, M. A., “The Influence of Geometrical and Operational
Parameters on Thermofluid Performance of Discontinuous Colonial Self-swirl-inducing Baffle Plate in a Tubular Heat Exchanger,”
Heat Transfer, 2023.
24. ASHRAE Handbook Fundamental, American society of heating,
Refrigerating and air-conditioning engineers, SI-ed., Inc., Atlanta,
chap. 13, 14-15(1993).
25. Coleman, H. W. and Steele, W. G., “Experimentation, Validation,
and Uncertainty Analysis for Engineers,” John Wiley & Sons,
2018.
26. Cao, Y. Z., “Experimental Heat Transfer, first ed. National Defence
Industry Press, Beijing 1st ed., 120-125(1998).
27. Gnielinski, V., “New Equations for Heat and Mass Transfer in
Turbulent Pipe and Channel Flow,” Int. Chem. Eng., 16, 359-368
(1976).
28. Dittus, F. W. and Boelter, L. M. K., “University of California at
Berkley,” Publication on Engineering, 2, 443(1930).
29. Blasius, H., Das Ähnlichkeitsgesetz bei Reibungsvorgängen in
Flüssigkeiten, Forschungsheft des Vereins Deutscher Ingenieure:
Berlin, Germany, 131(1913).
30. White, F. M., Fluid mechanics, McGraw-Hill, Boston (2003).